Industrial productivity is a crucial factor in the success of manufacturing operations. Maximizing equipment uptime, minimizing downtime, and optimizing maintenance practices are key goals for manufacturers aiming to stay competitive in today’s rapidly evolving industrial landscape.
In this context, predictive maintenance has emerged as a game-changing approach that leverages advanced technologies and data analytics to proactively manage equipment maintenance.
In this article, we will explore why predictive maintenance is considered the future of industrial productivity, highlighting its benefits and the transformative impact it brings to manufacturing operations.
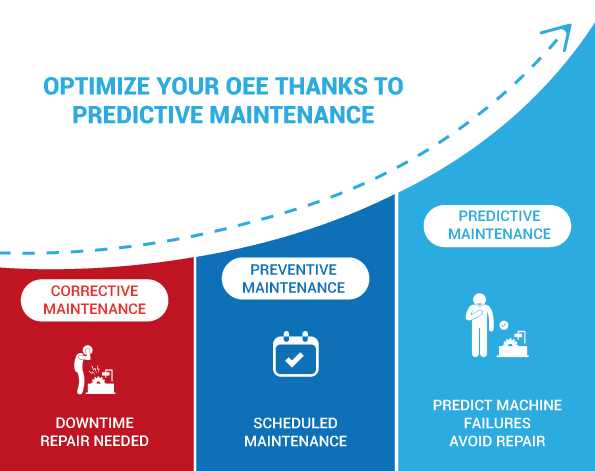
Minimized Downtime and Production Losses:
Predictive maintenance enables businesses to anticipate and address potential equipment failures before they even occur, minimizing unplanned downtime and production losses. By utilizing real-time data, sensors, and predictive analytics algorithms, industries can identify subtle changes in equipment performance that may indicate an impending failure.
This allows for proactive maintenance measures to be taken, such as scheduling maintenance during planned downtime or addressing issues during off-peak production periods. By avoiding unexpected breakdowns and reducing downtime, businesses can maintain a continuous and uninterrupted production flow, ultimately maximizing productivity and profitability.
Optimized Maintenance Strategies:
Traditional maintenance approaches, such as corrective or preventive maintenance, often involve routine inspections or replacing components based on predefined schedules. Predictive maintenance takes a more data-driven and condition-based approach.
By continuously monitoring equipment performance and analyzing real-time data, predictive maintenance algorithms can detect patterns and trends, enabling businesses to optimize maintenance strategies.
This data-driven approach helps determine the optimal timing for maintenance activities, ensuring that maintenance is performed only when necessary, minimizing unnecessary downtime and reducing maintenance costs.
Improved Equipment Reliability and Lifespan:
Predictive maintenance enables businesses to gain deeper insights into the good condition and of their equipment. By monitoring critical performance indicators, such as vibration, temperature, or lubrication levels, businesses can detect early signs of equipment degradation or abnormalities.
This early detection allows for timely interventions, such as adjusting operating parameters or replacing worn-out components, ensuring that equipment operates within optimal conditions. Consequently, equipment reliability and lifespan are improved, reducing the frequency of breakdowns, increasing overall equipment efficiency, and extending the useful life of assets.
This leads to significant cost savings and improved return on investment (ROI).
Enhanced Safety and Risk Mitigation:
Equipment failures can pose significant safety risks to workers and the overall production environment. Predictive maintenance plays a vital role in enhancing safety by identifying potential risks and taking preventive actions. By continuously monitoring equipment conditions and performance, businesses can detect anomalies or safety hazards, allowing for timely maintenance or interventions to mitigate risks. This proactive approach reduces the likelihood of accidents, injuries, and costly incidents, fostering a safer work environment and ensuring compliance with safety regulations.
Data-Driven Continuous Improvement:
Predictive maintenance generates vast amounts of data from various sources, such as sensors, equipment logs, and historical records. This data can be leveraged to drive continuous improvement initiatives. Advanced analytics and machine learning techniques can extract valuable insights from the data, identifying patterns, correlations, and optimization opportunities. These insights can be used to refine maintenance strategies, improve operational efficiencies, optimize equipment utilization, and identify opportunities for process optimization.
By embracing a data-driven culture, businesses can unlock the potential for continuous improvement, ultimately driving industrial productivity and competitiveness.
Predictive maintenance is revolutionizing the way businesses manage equipment maintenance, making it a cornerstone of future industrial productivity. By leveraging real-time data, advanced analytics, and predictive algorithms, businesses can proactively manage maintenance activities, minimize downtime, optimize maintenance strategies, improve equipment reliability, enhance safety, and drive continuous improvement. Embracing predictive maintenance enables businesses to stay ahead in a rapidly evolving industrial landscape, ensuring maximum uptime, optimal asset utilization, and sustained productivity gains.